corrugated plastic roofing, polycarbonate roofing, fiberglass roofing
Corrugated plastic roofing is not intended to be a main house roofing system, but rather it is very useful for smaller roofs around the home.
Introduction
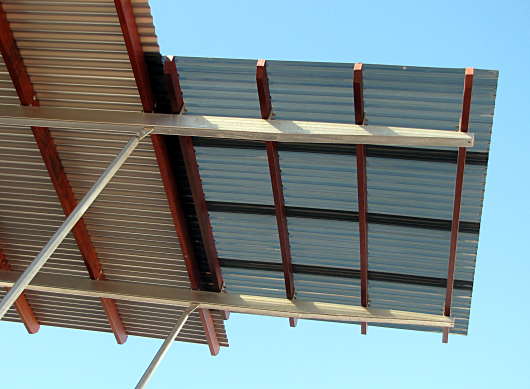 |
Corrugated plastic roofing that matches the profile of the main steel roof. This is an extra feature roof to give shade and shelter to an outside flight of stairs |
Many of these products are manufactured to share the same profile as similar steel rolled formed sheets. It does not mean however that they are as strong and caution should be used when walking on roofs with these products as I have seen some that are extremely fragile looking when new and downright dangerous when aged and affected by sunlight.
That being said there are a lot of very strong and good looking products that are excellent for their purpose.
- There are a series of very strong commercial grade fiberglass sheets that are made specifically for very corrosive environments. The factory that I go to that does hot dip galvanising has had it's steel roof replaced at least twice to my knowledge. Why they don't replace the sheeting over the caustic or acid cleaning baths with fiberglass I don't know.
- Apart from strength there are also many different colours and transparency ratios. From clear though grades of translucency to opaque. Some of them that filter UV but still let plenty of light through.
- A few times I have done an addition to an existing house that consists of a roofed patio or verandah. I live in the tropics, so we do many of these for outside living areas and shade, so we use steel sheeting. When the new roof is completed it sometimes shades the kitchen window, so we put a couple of sheets of corrugated plastic roofing that is the same profile as the steel roofing to allow natural daylight to get into the kitchen again.
- After doing a couple of these I have come to the conclusion that a single sheet of clear or semi opaque sheeting would make an excellent substitute for a skylight. It may not look as good as a skylight, but it could possibly be only a tenth of the cost.
- Some manufactures standardise on smaller sheets say 1800 (6ft) long and actually call them corrugated plastic roofing tiles. Others make sheets up to 3000 (10ft) long.
- In temperate climates these translucent sheets can provide soft filtered light for decks and sun rooms.
- Many of these products are excellent for greenhouses and they are a cheap alternative to glass.
- All of these corrugated plastic roofing products have a large thermal expansion rate, compared to most other roofing materials. FRP (fiberglass reinforced panels) at a lesser rate than Polycarbonate and PVC panels.
Back to top
Fixing tips
- Some of these corrugated plastic roofing panels will not hold your weight if you stand between supports, you must read the manufacturer's instructions in regard to correct fixing.
- Wear safety glasses when using power tools. The small chips really fly on some of these brittle materials.
- A barrier cream can stop the itch effect when cutting fibreglass corrugated sheeting.
- Because of their large thermal expansion rates these products should have their fixing holes pre-drilled at least 2mm larger than the fixing screws.
- Polycarbonate sheets have a UV resistant layer on one side of the sheeting. This layer faces the sun and each sheet is marked which way to fix.
- Follow the manufacturer's recommendation's for fixing screws, washers and seals.
- Don't over tighten. Set the screw gun so that you can slowly wriggle them in, stopping as soon as the seal grips the sheet.
- Don't store a stack of translucent sheets in direct sunlight. They can build up a terrific amount of heat and this can cause a clouding effect in the sheet which can not be removed.
- Some of the thinner sheets can be cut with a sharp hand saw, and I have also used tin snips for small cutouts. These thinner sheets can also be cut lengthwise with a utility knife.
- Thicker sheets need to be cut with a power saw. Use the finest toothed blade that you can find. Using a coarse blade can cause splinters to fly and leave a very rough edge.
- A normal HSS drill bit will drill the sheets easily if it is kept sharp.
- As a general rule try not to drill too close to the ends. I like to arrange the purlins so that end holes are about 100 (4") from the end.
- Another general rule is to keep the purlins a lot closer together. Like 600 or even at 450 centres, but take the manufacturer's advice on this for your area.