|
Concrete tools
Concrete tools, used in laying, spreading, leveling, vibrating and finishing concrete. They range from something like a wooden float that you have made for yourself, though store bought screeds and bull floats to machine driven vibrators and helicopters.
Hand tools, floats and edgers for concreting
Always on the job somewhere are a a few square mouth shovels, a wheelbarrow or two, and a couple of rakes. At a pinch you can manage without rakes, just use the shovels, but a nice rake makes the job easy.
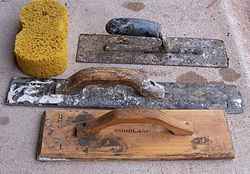 Concrete tools - hand held floats.
|
Here are three floats, rectangular steel float, my old magnesium or mag float and a cheap wooden float. The mag float is the only one I would use now, if I had a small job to do I would buy a new steel float, like the one below. The one here should have been thrown out years ago, as it no longer has that smooth slightly convex curve to the face. On the subject of steel floats, at the hardware store, make sure you don't pick up a plasterboard fixers jointing float by mistake, they have a slat surface, but the edge is ground convex for the tape joints.
|
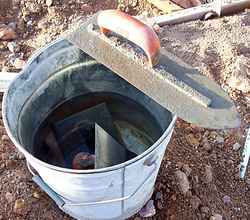 Concrete tools - Steel float
|
Here is the favourite type of steel float. The curved point at the front gets a fair bit of use. All new steel floats are a joy to use, and then gradually they get used for things other than intended. They should not be used for scraping or chipping hard concrete off formwork etc.
Don't ask a concreter if you can borrow a float. That's like asking a roofer for the loan of his snips. If he is a polite sort, he will only tell you to p-ss off!
Like most tools, steel floats do a good job only as long as they are looked after. Once they are twisted or kinked they are useless for finishing.
The galv. bucket is always handy, they last for years if you keep them clean and can be filled up with concrete without fear of them breaking like plastic buckets do.
|
 Concrete tools - Rounded ends steel float and a flexible steel Shotcrete cutter.
|
Here is a shot of another popular type of steel float that I have lifted off my Shotcrete page.
|
Concrete tools - hand edger.
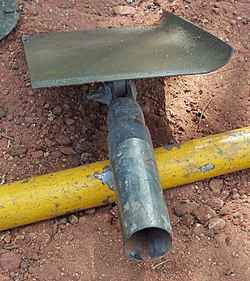 Concrete tools - walking edger.
|
On the right is a hand edging tool, about 100mm wide, and below right is a similar one that can be fixed to an extending aluminium handle. Sometimes called a walking edger
It seems to me that maybe I should be calling both of these tools bull nose edgers, because they have a decent curve to the edge. Smaller ones only have something like a 6mm radius. Using these it is essential to run them along the edges fairly soon to push the aggregate down.
|
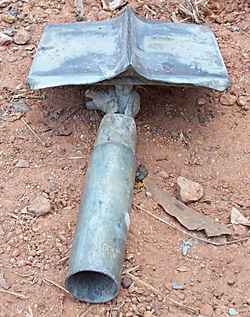 Concrete tools - Walking jointer.
|
Here is a joint tool that can also be used on a pole. I have never used a pole for edging or jointing, but I guess that the old finisher who once told me that "broom finish is the only way to go", because "you don't have to bend your back" would say the same about these things.
When using a jointer, you have to lay a straightedge, like a board or a screed on the surface of the wet concrete to give you something to work to. It is impossible to make it look good working freehand.
|
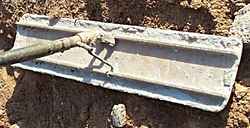 Concrete tools - Mag bullfloat
|
A store bought magnesium bullfloat. I have no idea where the name comes from and I don't really know who invented them, but the first one I ever saw was owned by an American guy.
If the handle is twisted anticlockwise you will see that the edge nearest the operator will lift up. When twisted the other way the other edge will lift up.
If the concrete is a touch on the dry side, a trick that sometimes helps to bring the moisture and fat to the surface, is to jig it backwards and forwards to work the surface. This leaves a series of ripples, which are easily leveled with a couple of smooth strokes.
Another thing that I have seen done is to add a bit more weight to the float in the form of a couple of bricks, but only when the stuff is going off fast and things get a bit desperate.
|
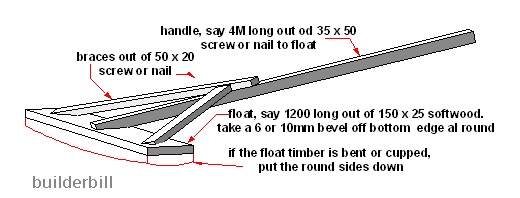 Concrete tools - Sketch of home made bullfloat
Here's a sketch of a home made bullfloat that I have made quite a few times, when I have had to do my own concrete finishing.
Usually a length of ceiling batten for handle and softwood for the float itself. Mostly I nailed them together and threw them away after the job was finished.(used the batten on a ceiling most like). That's why I needed the braces on them, but if I had to do a few days work with one I might make something a little more permanent.
Lay the float timber on a flat surface and rest the handle on it, get a mate to hold the end of the handle (or pack it up) just above waist height. Use a bit of scrap to scribe the cut. It will be a fairly long raking cut but you don't have to be too fussy.
In use, pushing away from you hold the thing about knee height so that the front edge is up a bit. Coming back, hold it about head height. If the site is clear it is simply a question of walking backwards and forwards. Easy peasy!
Don't think that this is in any way inferior to the bull floats shown on these pages. It does just the same job. The timber one in some cases is better than the mag one, not quite as much bleed water is brought to the surface and so it is better under certain conditions. (Air entrained concrete, cold climate stuff).
The shop bought ones have convenience built in. The handle extends, the head is detachable for easy storage, the blade can be tilted.
So if with your home made one you are cramped for space in an area, cut it shorter or make another. If you have a footpath to do that is 1100 wide, make on to suit.
|
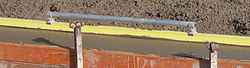 Concrete tools - Aluminium screed.
|
Here is a standard shop bought aluminium screed. This one is a 3M long extruded aluminium box section with plastic end caps. The handle makes it very comfortable to use. They come in various lengths, but the maximum I guess would be 3.5M. It is after all a one man tool.
A screed can of course be any material, as long as it is straight. One man screeds of necessity have to be light, so pine timber is OK, with aluminium box section as the favourite.
In use the screed is tilted slightly with the leading edge raised a few mm. This gives a smoother surface to the concrete.
When I first worked on a concrete job as a formwork carpenter in the early sixties aluminium screeds were unheard of. We had to select or make straight lengths of timber, say 150 x 50 for the concreters. The screed was invariably rested on the top of the formwork with a man at each end. Quite often we would have vertical bits of dowel as handles at the ends.
The technique was to tamp the screed up and down on the top of the wet concrete surface, leaving a row of ripples. This compacted to surface and brought the water and fine to the top. Then a sideways traverse with a sawing backwards and forwards movement leveled it off.
|
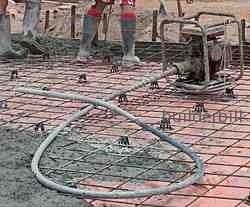 Concrete tools - Petrol vibrator.
|
Here's a standard petrol engined flexible shaft immersion vibrator. The shaft is 1 1/4", 30mm. The engine and shaft are bought separately and because the connection is an industry standard, the a shaft will fit all this type of engines. This is by far the most common one seen on building sites.
Smaller versions are available, with single phase electric motors, driving smaller shafts. You would maybe hire or buy one of these if you were doing some small pre-casting work. The last time I used one was on a purpose built polished concrete wash trough. The small needle vibrator got down into the thin wall sections and did a good job.
|
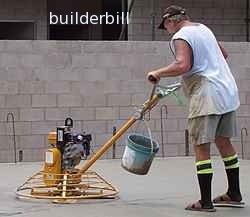 Concrete tools - Power float or helicopter
|
Here is a petrol engine driven power steel float, commonly called a helicopter. These are again always about the same size. They have lifting handles at each side, and it takes two men to place them on the slab, carefully.
The motor has an automatic clutch, so that when it is started, the blades do not move until the revs are increased.
With the handle held level it is possible to walk forward and backwards. Lift the handle slightly and the machine moves to the left (opposite direction to the blades travel) and lower the handle and it goes right. Experienced hands always have a laugh at the expense of guys handling one of these for the first time. It is a definite skill, but does not take too long to pick up. Just don't practice near an edge that could damage the machine if it went off.
The blades are adjusted by a small handle that when spun round, lifts or lowers the steel blades. Have them higher at the beginning, and as the surface hardens, lower them for a denser and more compact shiny finish.
Note, the guy in the photo is doing a final float with a bucket of water and a sponge to put a drop of water now and again to help him polish out imperfections. This was in the middle of an extremely hot day, but he should not have been doing it. Adding water to aid in floating can make the finished surface flaky or powdery.
|
|
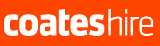
Hire Equipment
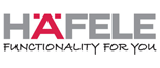
Furniture Fittings - Architectural Hardware - Electronic Locking Systems - Technical Hardware
BuilderBill sponsorship
Joints in concrete flatwork
|