Concrete Basics
The page title says it all, concrete basics. So as you can imagine, here I will give you a brief overview of the basics of small concreting jobs that owner builders and home renovators might want to tackle themselves. This overview should give you enough information to talk to contractors and understand the ways that we get good concrete. I will not go into great detail, there are many technical websites out there that do that. In my usual way I will try to give you some of the more practical things that come to mind.
Back to top
What is concrete
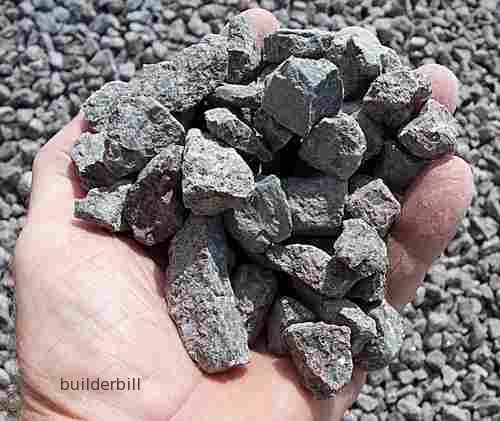 |
Concrete basics - Aggregate or crushed rock for concrete |
Above is a hand full of concrete aggregate. It is clean, sharp, and hard crushed rock, that is perfect for making good concrete. The course texture and sharp edges allow it to bond well to the other ingredients giving a stronger mix than rounded pebbles or softer rock would do.
Modern concrete started with the introduction and manufacture of Portland Cement in England around 1842. There are many variations of concrete, but the basic concrete that will be delivered from a local batching plant by a transit mixer (the truck with a rotating bowl on the back), or that you may mix yourself on site, consists of the following ingredients.
- Standard grade, general purpose, grey Portland Cement. Sold in bags of around 20 kilograms.
- Crushed rock or aggregate, of various sizes, graded to give a selection from the largest to the smallest.
- The largest size of aggregate depends on the work being done. The concrete has to act like a fluid packing tightly around rebar and fitting neatly into corners.
- On large civil engineering structures the size may be quite large but in general the transit mixers that we see in our cities and towns will be using a maximum size of 20mm or 3/4".
- Certain jobs like paving work may use a maximum size of 10mm or 1/2"
- There may be one or two intermediate sizes of aggregate and the the smallest aggregate in the mix is sand.
- The finest particles in the mix are provided by the cement.
- There has to be enough cement in the mix so that when it is combined with the water there will be enough cement paste to coat every piece of aggregate to make a homogeneous mass.
- Clean freshwater. It has been said that the water in concrete should be good enough to drink.
Back to top
How to order ready mixed concrete.
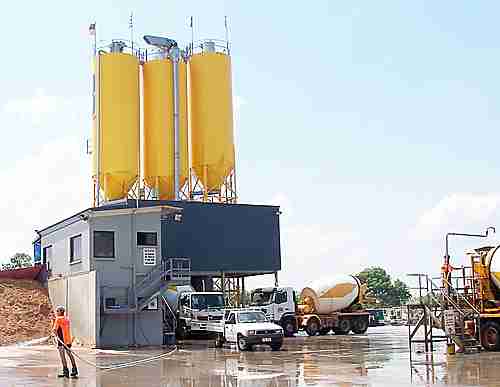 |
Concrete Basics - A concrete batching plant for ready-mix concrete trucks> |
When you ring up the concrete supply company they will want know a few things, apart from the obvious where you live and when you want it.
- How much you require in cubic metres. This is in increments of 0.2cuM. So on a small job you may order 0.8cuM or a larger job 3.4cuM.
- What the concrete is to be used for. Footpath, house slab, footings etc. A footpath will probably use what we call a paving mix, with a maximum aggregate size of 10mm where a driveway will be thicker and 20mm will more likely be used.
- The strength of the concrete. On say a house slab, you will have on your drawing or in the specifications somewhere "Concrete class N25". The different classes denote the strength of the concrete, so N25 will be normal class, that has a normal workability and has a compressive strength of 25MPa or around 3600 pounds per sq inch after 28 days. (It's not 25MPa when your pour it, but it will be after the normal testing period of 28 days) Concrete gets stronger as it gets older.
- Placement method. The concrete batcher will want to know how you will be getting the concrete to the job.
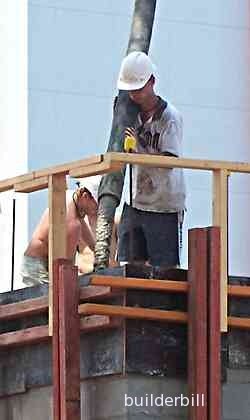 |
Concrete Basics - The mix for pumping is generally more liquid and contains a greater percentage of fines and cement slurry, to allow it to be pumped. |
- Concrete that is pumped will be designed for pumping, the batcher will then want to know the pumping company and the two will liaise with each other. Usually the pumper will radio the batcher so that the transit mixer will arrive just when the pump is set up.
- Placing straight out of the mixers shoots. Easy and quick if you can get the truck close to the job
- Wheelbarrow, not so easy and definitely not so quick. If it is a few cubic metres and is going to be slow the batcher may give you more retarder in the mix to give you more time to work it.
- On a large pour with more than one truck he may want to know the interval to send the trucks. Back to back or half hour intervals.
Another consideration with transit mixer trucks is the size. Quite often it is possible to get a small Mini-Mix type truck capacity 1.6 cuM around the back of a house, when a larger truck would mean a tough wheelbarrow job or a pump hire.
Back to top
Concrete Basics - Mixing on site.
Mixing concrete on site sometimes is the only way to go, even though it is less convenient and usually costs more than ready mixed.
- The location is just too far away from the batching plant.
- Once the materials are combined the setting of the concrete begins, the mix will inexorably start to set. It will not remain plastic after a certain time. So the farther away from the plant, the less time you have to do the job.
- I have done one job at a remote location, where we added the water and cement on site, to the previously batched aggregates in a transit mixer. Expensive but it worked well for a one off job.
- The dread of all concrete truck drivers is to have the concrete set in the bowl. Tell me about it! I once had a truck with 6cuM on board bogged at the end of an airport runway. Happy days.
- Some jobs are very hard to do in the large quantities that a truck brings in. You may need just more time to do the job.
- Mixing on site allows you to set your own pace and make adjustments as you go along. You can add your own colouring, strength or waterproofing admixtures, feature aggregates etc.
- Quite large paving, kerbing or pre casting jobs can be done by just one man, working at his own speed.
- Buy or hire a concrete mixer to do the actual mixing. They come in various sizes.
- The smaller ones have electric motors and are very convenient.
- The larger ones need the extra power that a petrol or diesel engine will deliver.
- A mixer should be loaded up just right. By this I mean that if you buy a 3 cu ft. mixer, then mix 3 cu ft. Don't try to fit in 4 cu ft. It might fit in, but it will take ages to mix, or not do the correct job.
I won't go into the specific details of mixes here, because there are so many combinations of what you may be doing and the materials available to do it. By far the best way is to get the proportions from your own material supplier.
- Our local supplier will deliver what we call pre-mix. That is the aggregates and sand have been mixed at his depot, so there is no need for separate piles of stone and sand.
- The mixing ratios are batched using the volume method. Ready mix companies measure the mix ingredients by weight.
- It is so common, to just measure shovels full, and throw the materials into the mixer that way, but this is very inaccurate. Try always to measure the volumes, except for trivial jobs.
- I have done jobs where we made up ply volume boxes, but an easier way is to use metal buckets. clean empty 10 litre paint tins or similar.
- At the least, use a bucket to measure the cement and water. The water cement ratio is critical.
- Try to keep your material clean and your bags of cement dry.
- The mix may be 2:5:7 with enough water to give a slump of 100mm
- That is 2 parts cement, 5 parts sand and 7 parts aggregate.
When mixing by hand, the amount of water used is usually, initially done by eye, then when a mix that gives the correct slump is made, the same amount of water is used every time after that to achieve consistent results.(Your sand and aggregate could be bone dry, or sopping wet, so that effects the amount of water to be used).
Back to top
Save Cash, Don't add too much water
One thing to remember, above all else, I know concreting is a hard job, mixing it, laying it and finishing it.
- Any of these operations can be made easier by adding water.
- DON'T DO IT! If you have a correct mix on site don't alter it.
- Adding water to a correct mix is like throwing $50 bills into it.
- If you are mixing on site, to give you a more workable mix, try more water plus more cement!
- Another alternative is the use of additives, contact your supplier for details of plasticisers etc that may make a difficult job easier.
- Concrete that has too much water in it dries out with more shrinkage cracks.
- It will not be as strong or have a hard wearing surface.
So once more to drive it home, you pay for a top quality product, don't waste money by ruining it with too much water.